Scanlon March 2004 E-zine
Greetings!
Our March E-Zine features several Conference related articles. You can learn about John Chipman, our 2004 Scanlon Steward, and you can also learn how Wescast gets the most from the conference experience. We also have an article about how Ferro is using the Lean Sim Machine internationally to teach lean concepts and a followup article on the recent Coordinators' Conference.
John Chipman Receives Stewardship Award

John Chipman Sr., founder of Landscape Forms, Inc., is the 2004 recipient of the Scanlon Leadership Network's Stewardship Award - the Network's highest honor. A dedicated servant leader, Chipman was selected based on his early and unfaltering support of the Scanlon Leadership Network combined with his numerous contributions to the organization, his industry and community for 35 years. John will be recognized on May 12, 2004 in Kalamazoo, Mich. at the annual Scanlon Conference.
"I am so grateful for this honor," Chipman said. "Although I hesitate to place myself in the same league as the other recipients, I appreciate it very much. I believe that this award is partially a tribute to me, but also a tribute to the company and all of the talented and dedicated employees at Landscape Forms. We have a marvelous company and fabulous people," Chipman added. "I know that Landscape Forms would never have succeeded as it has without the special guidance and attention given by Bill Greenwood and Carl Frost, as well as the support from the entire Scanlon Leadership Network."
As a Michigan landscape architect, Chipman founded Landscape Forms in 1969 to avoid laying off his seasonal landscaping employees during the long Midwest winters. John put them to work in his barn making well-designed, high-quality public space and site furniture at a time when virtually none was available. From this humble beginning, Landscape Forms is now headquartered in Kalamazoo, Mich. with more than 200 employees and leads the nation in the production of outdoor commercial furniture.
Held in high-esteem by colleagues, competitors and past Stewardship Award recipients, Chipman's nomination was enthusiastically supported by the Scanlon Leadership Network and its members. "I can think of no other commercial enterprise whose beginning derived primarily from its founder's commitment to employees' security and welfare," said William Greenwood III, management consultant. "I am always struck by how John's genuine loyalty and affection for the Landscape Forms' 'family' is reciprocated. I have observed no other President, CEO or Chairman more universally-admired and loved by his people than him."
Greenwood added that John was a major influence in his own professional and personal development, skillfully teaching him that there are "no substitutes to listening to people, understanding where they are coming from, and adjusting style appropriately."
"I consider John to be one of a few 'Quiet Giants' in establishing and exercising stewardship in his personal relationships and professionally to his Landscape Forms Company," said Dr. Carl Frost, Michigan State University Professor Emeritus. Frost, who first invited John to the annual Scanlon Conferences, compares Chipman to John Donnelly, founder of the Donnelly Corporation, Hugh DePree, former CEO of Herman Miller, and Charles Conrad, founder of Thermatron. "He is a willing, competent and committed servant leader, a 'giant' executive, organizational professional, and community steward," Frost added.
Dwane Baumgardner, Vice Chairman of Magna Donnelly Corporation, said, "I believe the value of John's leadership and contributions are evident in the quality of Landscape Forms' long-standing management philosophy, its people, and the company's outstanding performance over the years." Greenwood, Frost and Baumgardner are each past Stewardship Award recipients.
Chipman graduated from Michigan State University in 1953 with a degree in landscape architecture. After graduation, John practiced landscape architecture in Kalamazoo, Mich. from 1954 until 1969 when he established Landscape Forms, Inc. In 2002, Michigan State University honored John with the Landscape Architecture Alumnus of the Year award. Each year, MSU selects an alumnus from the landscape architecture program that has made a significant contribution to the landscape architecture profession, the environment, or to the university and its landscape architecture students. Additionally, the John Chipman Scholarship Endowment for Overseas Study provides opportunities for students in the landscape architecture program to expand their horizons through study abroad programs.
Ferro Uses Lean Simulation in Global Effort
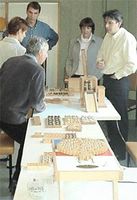
The Scanlon Leadership Network's Lean Sim Machine is being used by member firm Ferro Corporation of Cleveland to train trainers and employees in plants around the world in Lean Manufacturing techniques. The global initiative by Ferro is designed to make Lean Manufacturing a permanent part of the company's culture. The effort is helping Ferro improve the efficiency of its operations and is saving significant costs through improvements identified and implemented in the Lean Manufacturing process.
Ferro launched the global effort in November 2002 and has conducted training sessions in some 15 cities in seven countries. Hal Musler, Worldwide Director of Manufacturing for Ferro's Color & Glass Performance Materials business who is spearheading the global effort for the company says, "Ferro's Lean Manufacturing initiative is paying off in improved customer satisfaction and product quality, reduced cycle times and dependence on inventories. Through Lean we have eliminated a significant amount of non-value-added activity. Overall, we have reduced costs, improved operating performance and have reduced the level of working capital required to operate the business."
Scanlon Associate Consultant Rob Ptacek helped Ferro launch its program and has assisted Ferro's Ray Uniejewski with some of the training sessions. Uniejewski is conducting the worldwide training program.
"We use the Lean Sim machine in every training session," says Uniejewski. "It is an excellent hands-on tool that helps our people quickly learn the concepts of Lean Manufacturing regardless of the country they are in or the language they speak." The global initiative is a continuing process and more training sessions will be held in Europe and Asia this year.
Wescast Puts Conference Information to Work
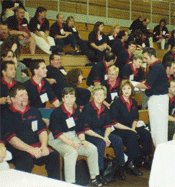
For many years member firm Wescast Industries, located in Canada, has sent 30 to 40 employees each year to the Scanlon Leadership Network's Annual Conference. They attend a variety of the workshops held at the Conference, not all of which may be directly related to their jobs. This gives Wescast personnel the opportunity to learn about a variety of topics related to the Scanlon Principles and a broad look at how other companies are applying the Principles. The formal aspect of applying the information when they get back to their jobs takes place at their monthly Business Information Meetings (BIMS). This is where the employees who attended the Conference make presentations in each plant to all shifts. This provides all employees an opportunity to gain an understanding of the general session and the content of the workshops.
"Although we are not big on formalities, our employees are very good at taking the information they learn at the Conference and sharing it with others," says Dave Bullock, HEART Coordinator for the WCB plant in Brantford, Ontario, Canada. "For example, one of our members attended a workshop at the last Conference on recognition and motivation of employees. She came back with several ideas and we have begun to implement some of them this year. We had to request a budget to implement the program but it was a good reminder that we can recognize employees in additional ways, not just through the gain sharing cheque.
Another employee from our plant attended a workshop on Equity and the formulas and measures used by other companies. Once each quarter, we review one of the Scanlon Principles and this fit perfectly in our discussion of the Equity Principle. The information our colleague shared gave us a better understanding of how the formulas, targets and measures work together. In addition, we are always looking for ways to improve our team building and communications even though we already do a pretty good job in these areas. Each of Wescast's five plants determines who goes to the Conference and the criteria for selection. At our plant we choose one member of the Plant Leadership Team, two front line leaders, and two HEART representatives."
Allison Letteau, HEART Coordinator for the Wingham Casting plant in Wingham, Ontario said, "One of the main things we do - we regroup to see what we learned - what we got out of the Conference and who we should share the information with. People may go to workshops that do not apply to their jobs. We highlight the information that is value-added and send it to the appropriate resources. We generate a presentation for BIMS and communicate what we got out of the workshops and what the next step should be. For example, if someone goes to a safety workshop, they talk to the safety department and pass on the information they learned.
"We always try to apply the information about team building, recognition, and communication. I always find the Conference helpful in providing information on building teams, developing team leaders and how to get teams working together better. We learn what other plants are doing and we can compare our programs with theirs. We are always looking for ways to make our programs better. It is also good to learn that there are other companies out there facing the same issues we are and how they get around the hurdles they encounter.
"In addition, we are always seeking better ways to measure HEART suggestions. At the Conference we often learn about an idea that we can take back to our plant that will help improve participation. We get ideas for employee recognition that we can use. We also learn how other member companies are applying the Scanlon Principles and that may give us some ideas on how we can do things differently."
Coordinators Give and Take At Coordinator's Conference

The Scanlon Leadership Network describes its logo with phrases such as teamwork, connectedness, two-way and forward together. These same words were exemplified at the 2004 Scanlon Coordinator's Conference, themed Tools for Scanlon Excellence. Hosted at SGS Tool Company in Munroe Falls, Ohio, the annual Coordinator's Conference is designed to offer networking opportunities to new and old members alike, providing a forum to receive tips from peers and exchange ideas.
"Since we are just beginning this process, the Coordinator's conference was really useful," said Lydia Morales, Human Resources Development Manager at National Manufacturing Co. in Mexico. "We will be the first company in Mexico to join the Scanlon Leadership Network. Watching others become so enthusiastic about our plan was particularly encouraging."
"The reality is that every organization faces some challenge with its plan," said Sylvia Hurst, QUEST Coordinator at Smith Dairy, Orrville, Ohio. "The conference offers countless opportunities for one-on-one question and answer sessions with other coordinators. These conversations prove to be invaluable. Speaking with SGS Tool Company's panel of associates was extremely beneficial. It was clear that their responses were not scripted - they were very straightforward and told it like it was. Plus, hearing SGS President and COO Tom Haag share how and why his company and its associates benefit from Scanlon was the icing on the cake!"
The benefits, ideas and energy from the conference are put into action once participants return home. "I'm trying to keep the Scanlon principles in the forefront with newsletter articles, bulletin boards and PowerPoint presentations," said Hurst. "It was also a thrill once we recognized how simple it is to apply HOSHIN - a quick and easy way to see the measures and address accountability issues. I plan to create a HOSHIN spreadsheet for the coordinator position."
"Sharing my experiences about this year's conference helped others get an overall vision of the Scanlon principles and how this can work for us," said Morales. "They are beginning to understand that Scanlon won't work by itself - it needs our employees' support to move forward. Culturally, we are different from American and Canadian companies. This will not be an easy road, but we are working on it - and thanks to the Coordinator's Conference, we're excited about it too."