Scanlon May 2004 E-zine
Greetings!
This E-zine contains information about the exciting Scanlon work National is doing. A best practice game from National of Canada for increasing cost saving suggestions is described. (It is further described in the 2004 Best Practice Books). Fanal's (National of Mexico) efforts to develop the first Scanlon Plan in Mexico are also featured. Our 2004 Best Practice Books are in the mail. Our "Conference on a Disk" that features videos and handouts from the 2004 Conference will be mailed next week to members who attended the conference.
National's Mexican Subsidiary Installing First Scanlon Plan in Latin America
Fanal, a wholly owned Mexican subsidiary of National Manufacturing, is in the process of installing the first Scanlon Plan in Latin America. Located in Monterrey, Mexico, three hours south of Laredo, Texas, Fanal has 1,100 employees and produces padlocks, door sets, screws and other builders' hardware products.
National Manufacturing, which bought the company in 2000, is headquartered in Sterling, Illinois where it has two facilities and two in Canada with a total of 1,000 employees in the two countries. The company, which has manufactured hardware for more than 100 years, has had a Scanlon Process in place since 1979. Since its inception Scanlon bonuses for employees have exceeded $50 million for the US facilities.
When they were considering the possibility of installing the Scanlon Process at the Mexican facility, National Manufacturing's CEO Keith Benson and Bill Medland, Senior Vice President of International Operations, wondered if the participative process would work in the Mexican culture. They decided to move ahead with the help of Scanlon consultant Bill Greenwood who was intrigued with the challenge.
Medland, who is responsible for National Manufacturing's Canadian and Mexican operations, says, "Our hope is that we will reap the benefits when the employees in the Mexican operation realize that we value their ideas and are counting on them to make suggestions that will help drive costs down and increase productivity. Participative management by tapping the resources of employees is a new concept in Mexico but implementing the process and making it successful won't happen overnight. It is going to take a couple of years."
The company started the Scanlon process in April 2003 with the help of Greenwood, who explained the principles and worked with the management team, exploring the concept of participative management. Traditionally at Fanal it has been management from the top down with a key group of management, professionals, front line supervisors, and sales management directing the operations of the company. Employees traditionally have not been involved in the decision-making process and their suggestions were not solicited.
"We have been working at this for a year now," Medland says. "We expect to have the first draft of the plan written by the end of this year and have an employee vote in 2005. We have been working with some 50 senior management and professionals at Fanal in regular communications meetings. Since only one third of the group speaks fluent English, we conduct the meetings in Spanish.
"When we started the process we worked with the four most senior members of management and were shocked to learn that, other than the senior finance person, these managers had never received the financial statements of the company," Bill added.
"In the first meeting when we showed them the numbers, there was genuine praise for sharing the information. The negative financial results helped them understand and accept the difficult decision we had to make to reduce the work force. We needed to share the financial reports with them to help them understand how they could drive the numbers up or down."
Employees have indicated an understanding and acceptance of the concept of employee participation but, "When they say yes, it doesn't mean they have internalized the information into true acceptance," Medland points out. "It has taken some time to convince them this is a serious change in operating culture and not just a cosmetic program. They have struggled with the changes that this will bring about, but now they know we are serious about it."
CEO Keith Benson reinforced the information the Mexican employees have been hearing and told them the Scanlon Process was a corporate-wide program that has been very successful for nearly 30 years.
Bill, who spends three weeks a month in Mexico, has four directors who are currently sharing the responsibility of running the operation. He expects to follow this schedule for at least another year and guide the process that will help employees achieve their goal of transforming the company.
"They want to change the name from Fanal to National de Mexico," said Medland, "and they are working hard to earn the right. I enjoy seeing managers come to the realization they have the right to stand up, say they don't agree with a decision or an idea and suggest an alternative. We are having success with this at many different levels. Some managers will sit across the table and go toe-to-toe with me. This tells me they now know that their opinions count especially when I say 'let's go with your idea'. When they are motivated and involved the best thing I can do is to get out of their way."
National Manufacturing Plays, Wins Gold
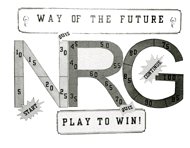
National Manufacturing of Canada earned a gold medal for participation with its "Way of the Future" NRG (National ReGeneration) game. Designed to increase participation and reduce operation costs, the game divided employees into six teams and challenged each to submit the most suggestions within a five-and-a-half month time frame.
"The NRG game proved to be a huge success for our company," said Brenda Eben, Scanlon Coordinator, National Manufacturing of Canada. "During the time we played it, our employees generated twice the number of suggestions versus the previous two years combined."
The result of a brainstorming session, the game encouraged employees to identify ways to improve all aspects of the company by making suggestions. Each suggestion was worth five points and although the highest possible score was limitless, a team needed at least 100 points to win. After a team earned 30 and 70 points, its members had to complete a quiz testing their knowledge of Scanlon principles and practices, safety procedures and company policies. Once all questions were correct, team members received company mugs and $25 gift certificates, respectively. The team that earned the most points by the end of the game received the grand prize of company jackets.
Founded in 1901, National Manufacturing Company is headquartered in Sterling, Illinois where it has two facilities plus two sites in Canada for a total of 1,000 employees in both countries. The Swift Current, Saskatchewan and Cobourg, Ontario locations have been part of National Manufacturing for 30 and four years, respectively.
As I See It - Tracy Pugh

Tracy Pugh, Sales Administrator, Pacific Cast Technologies, Inc., Albany, Oregon. Tracy has been with the company for nearly nine years and has been involved with Scanlon since the beginning, attending one Scanlon Annual Conference.
"The Conference was wonderful," Tracy said. "I was in awe of the number of companies and how they each implemented Scanlon. It was very exciting to see the possibilities and what can happen once everyone in the company is on board.
"The Conference also taught me that everyone has an important role at Pacific Cast and we need to recognize and appreciate that. We're successful because of each other. I think it's amazing to see an employee generate an idea or suggestion that results in a huge cost-savings for the company.
"Scanlon has also helped me look at what I do on a daily basis," she continued. "Instead of doing a task the same way out of habit, now I'll take the time to find a better, more efficient way.
"The most important thing to remember is that Scanlon is a way of life - not just a program. It's a way of life that can be applied in business or in your personal life."
As I See It - Rick Blood

Rick Blood, Finishing Operations Manager, Pacific Cast Technologies, Inc., Albany, Oregon. After four years with the company and seeing Scanlon at work day-to-day, Rick attended the 2004 Scanlon Annual Conference for his first hands-on exposure to the Scanlon process and its members.
"The Conference offers a ton of information," said Rick. "The only down side is you can't be in two places at once. There is so much to see and take in with people who are ready and willing to share their experiences and knowledge.
"For me, the key to Scanlon is communication. The Conference exposed me to other organizations that at some point have struggled with similar issues, like how to implement Scanlon or get everyone on board," he continued. "Conference participants continuously stressed that communication, participation and involvement are key to a successful plan and I agree with that.
"Scanlon is ultimately a culture change and that can be difficult to do. The concept of Scanlon is good and all of its members need to constantly develop ways to improve their companies. There are so many ways to do that and the annual Conference really helps you to see the possibilities."